Recycling Balers: Are They Right for Your Business?
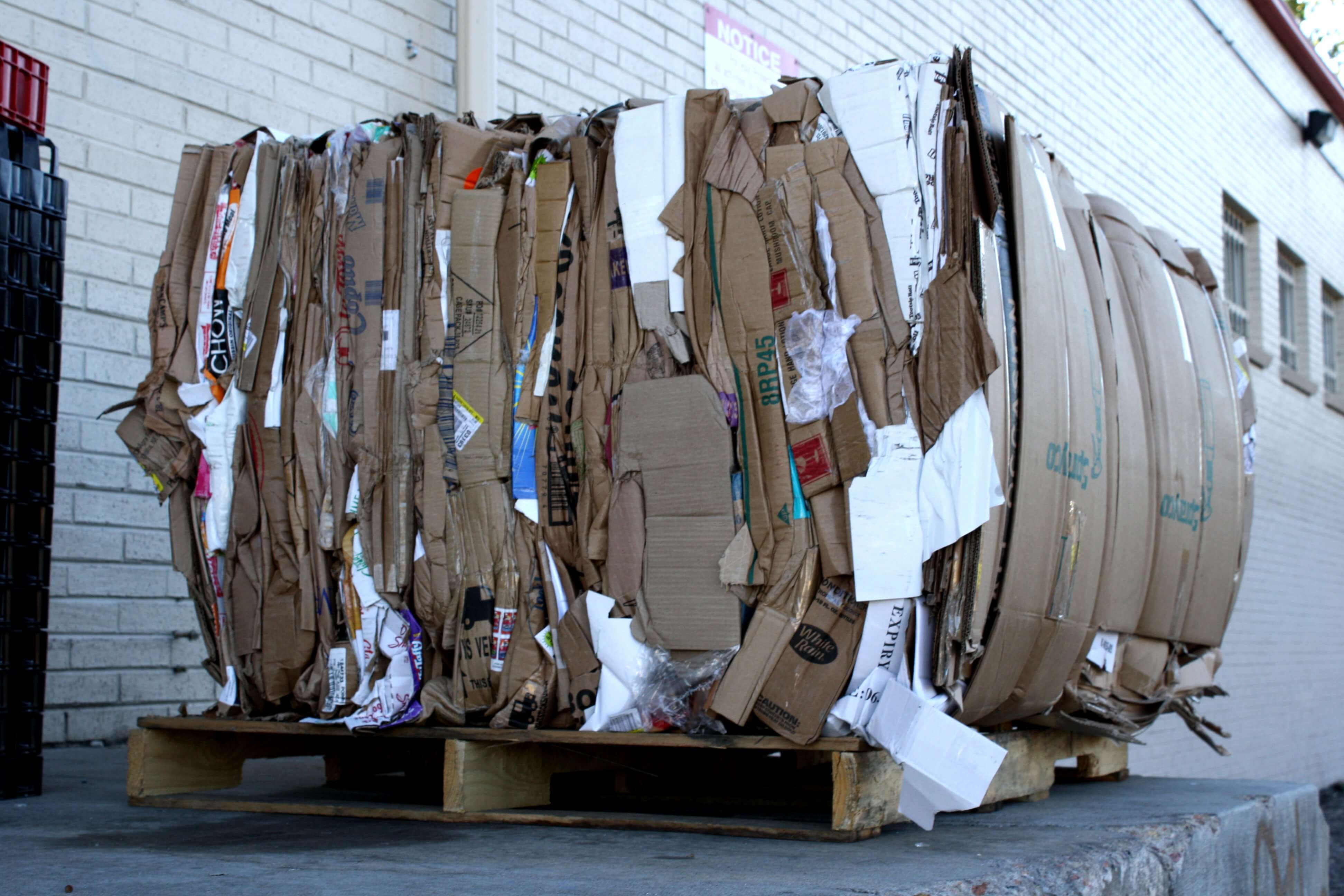
Balers are often integral to a company’s recycling program. Balers are industrial compacting machines that turn recyclables into blocks in order to be easily stacked and transported. These units can be an asset to businesses of any size and type due to the many benefits associated with their use, but not all balers are right for every business.
These machines help pack large amounts of recyclable material into a more compact shape, allowing easier storage and shipment. Smaller companies can benefit from not having to invest as much in other areas of waste management, such as collection bins. Additionally, larger businesses may be able to make some money by selling large quantities of recyclables to recycling companies. Companies such as retailers, restaurants, hospitals, and theme parks are ideal candidate businesses to implement a baler.
Types of Balers
There are three general types of balers. Vertical balers are designed for facilities that process a small number of materials to be baled. Typically, vertical balers have a much smaller output with a bale size of up to 1000 pounds. These balers are most commonly found in retailers where cardboard is the main material being baled. Horizontal balers are typically used in higher production settings, such as distribution facilities, recycling centers or material recovery facilities. They are best for companies that produce more than 100 tons of recyclables per month. While the vertical baler can usually produce one bale an hour, a horizontal baler can produce thirty bales an hour. They utilize greater thrust to compress the materials and the bales are automatically tied vs. manually tied on the vertical balers. For many facilities, these larger balers are not the optimal solution due to their price tag and space requirements. Instead, mini-balers may provide a solution to bring this technology to more companies.
The third type of baler is the mini-baler. While mini-balers do not have the capacity and crushing power of the larger balers, they are better able to handle smaller volumes of easily bale-able recyclable materials. For example, small cardboard boxes, plastic shrink wrap, and aluminum cans are each easier to bale than scrap metal. If your business is primarily recycling small volumes of cardboard boxes and plastic wrap, you likely do not need a vertical or horizontal baler within your operations. Some businesses are opting for mini-balers to handle their recyclables due to the numerous benefits and flexibilities they offer in comparison to the mini-baler’s larger counterparts.
Pros and Cons
Mini Baler Pros
Mini-balers create smaller, more manageable bales that are easier to handle. The small bales make it much easier to process and organize these materials for recycling, while also removing them from the facility’s waste stream. With fewer materials being sent to the landfill, you will also likely see your waste hauler costs decrease. With their small size comes a more affordable price point as well. Mini-balers can be purchased at just over $1000, while traditional vertical balers can range anywhere from $5000 up to $1 million. At their lower price point, mini-balers may be the solution for facilities that require a more flexible recycling solution. If you have several workstations each creating small volumes of recyclables, it may make more sense to have several mini-balers rather than one centrally placed large baler. Additionally, the physical requirements of a mini-baler may be easier to accommodate for many facilities. Mini-balers are an ideal solution when space is limited. They do not have the same footprint and height requirements that traditional large balers do.
Mini Baler Cons
However, this technology is not without disadvantages. Mini-balers inherently have less processing power, so they may not be able to process all materials. Cardboard and plastic wrap are the primary recyclables that can be processed, whereas aluminum cans, office paper, clothing, and other materials would not be a good fit for this technology. Additionally, some mini-balers may produce bales that are a nonstandard size, so it may be more difficult to find end users to purchase them.
Large Baler Pros and Cons
Large balers are able to process a much larger volume of materials compared to mini-balers. However, size is often a limiting factor for these machines. Vertical balers often need upwards of 12 feet of vertical space, and horizontal balers often take up 12 feet of horizontal space. A facility’s specific space requirements should be taken into primary consideration, particularly when factoring in space to move the bale after it has been compressed. Finally, the high price point may sway some businesses from investing. Large balers can cost anywhere from $5000 to $1 million. Many companies do report that they later recoup this investment through collection and container rental savings, but it is important to understand the upfront capital needed for this large machinery.
Real World Examples
Several businesses are already using recycling balers and seeing the savings roll in. DHL moved away from one large recycling container solution to two separate balers: one for cardboard and one for plastic. A Toyota dealership in Virginia uses its small footprint cardboard baler to save $700 a month on container rental fees alone. In nine months, Stone Bridge High School in Washington reduced the number of trash pickups by 40 percent, thanks to balers. The University of Mary Washington has saved time, energy, and money by baling their cardboard in house. Additionally, they were able to decrease the food cans, used reducing the volume and waste disposal costs by 90 percent. Nonstop, a computer retailer specializing in IT management, has seen the investment in their baler paid back within 12 months, due to high savings on collection costs and container rental.
Conclusion
Before any type of waste management equipment is introduced into a business, care should be taken to carefully evaluate the waste stream for key areas where recyclables are generated, as well as the volume and type of waste materials that might be the best candidates for baling equipment. Every business owner should consider these four factors before choosing a baler: the quantity of materials, the lifespan of the equipment, the type of materials, and the capacity to safely operate the equipment. Doing the necessary research will allow for maximum savings and environmental impact for your company.